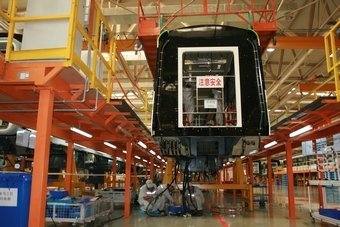
苏杭项目是总装车间精心打造的精益生产线,它再次显示推行精益产生带来的“新时速”:总装车间在苏州项目第12列车生产中试行4小时/节拍优化方案成功,至第13列车保持稳定节拍式生产状态,使苏杭项目从最初的无节拍生产,到三天、二天、一天半、10小时、8小时、6小时,至目前4小时/节拍的可控范围内,实现了精益生产新的飞跃。
运用精益工具,优化工位节拍。苏杭项目共计要交付82辆车,之前一天一辆的生产节奏远不能保证市场的需求,提速成为该项目的必然要求。总装车间运用精益工具,成立节拍优化实施督导组,采取作业写实,记录每个工位每道工序的作业时间、每位员工的作业内容和时间,绘制山积图和工序推移图,统计工位作业时间并发掘出整个工区的瓶颈工位、每个工位的的瓶颈工序。同时,重点对瓶颈工位、瓶颈工序进行分析、制定改善方案,对员工作业过程中存在的各种浪费、不合理工序、多余动作等进行发掘、记录并提出改善的方法,组织工艺员、人事管理员、工区长、工位长集体讨论改善方案,确定工位的节拍优化方案,与技术部沟通下发正式的技术通知对方案进行实施。
科学划分工位,优化组织能力配备。苏杭项目精益线A23工区共划分成14个工位,呈“U”形结构,有140多名员工,其中1-3年工龄的青工占全线员工的80%以上。年轻人有活力、学习能力强,但欠缺生产实践经验。针对这一现状,党支部充分发挥组织优势,在精益三项工程、IRIS贯标、精益工位建设等重点工作中带领和发动身边员工为精益建线出谋划策。树立示范工位,开展“名师带徒”,从提升员工的技能入手,强化质量六要素、作业要领书等技能培训和技术质量的专项培训。结合IRIS贯标,以推进精益工位质量管理为契机,建立安全质量防控体系、强化落实质量六要素,保证关键岗位有党员,党员率先承诺工位“四防”关键岗位,以实现重大质量事故发生率为零,零误差、零故障、零缺陷、保质保量高效完成任务。紧贴“三现”,落实党小组在工区的精益持续改善责任,党员提案改善率达80%。
健全流程管理机制,把控上下工序质量关。车间制定和实行了上、下工位交接的中间工序质量控制管理办法。通过《随车交接确认表》,对车上清扫状况、外观质量、产品配件防护和是否符合本工序开工技术条件等项目一一进行核对检查、问题描述和签字确认,完成交接,下工序才开始接料、送料上车,进行生产作业。这一管理机制,使质量责任明晰化,加速问题整改,有效把控上、下工序的产品质量,更加强了后工序为前道工序把关的责任和力度,增强了全员质量管控意识。
现场管理可视化,实现精益工具与流程管理有序可控。管理板由数字化配套图、生产计划、物料配套、计划兑现率、工区出勤率、工区零活统计、工区安全管理七大板块组成。管理板的建立使得工区管理更加简单化、标准化、规范化,基本实现了现场布局可视化;精益生产线工艺流程和工位工艺分工明晰、责任清楚;工位作业标准书或作业指导书文件化;工位六要素管理的强化与控制,使工位TPM活动的持续性、工作异常处理的快速性、5S管理的长效性、以及一次交验的合格率和日生产计划完成准时率均保障在有效可控中;工位安全地图的绘制和安全要素点检内容的完善明晰,使员工的安全保障意识明显增强,工伤的发生率大幅下降;技管人员要求“三现”主义,将点检、分析、处置、辅导等岗位职能融入每一天、每一个问题项点中,从而使车间精益工具与流程管理呈现出有序、可控、和谐的管理局面。
苏杭线自第14列车开始,以4小时/节拍的精益生产方式稳步按计划推进。总装车间下一步还将持续精益改善,深挖管理潜力,注重细节,将苏杭项目精益日产实现2辆作为新的奋斗目标,为搭建B型铝合金全焊接车精益平台提供强力支撑。
点评:
精益理念的有效运用不仅是生产线实现产量上涨的可靠保证,而且实现了质量与安全的同步。苏杭线精益生产实现了时间上的飞跃,也保证了产品的质量与安全。不仅如此,车间又为自己定下新的目标,继续推进精益,以实现产量更上一层楼。